Preventing Loss and Damage to Mission-Critical Gear Within Your Construction Supply Chain
The Impact of Lost and Damaged Gear
Regardless of the design specifications, data centers are comprised of integrated systems of high-value components and equipment. Each part of the system is vital to the successful activation and profitability of a site. If any essential components or equipment are damaged or lost, the impact to a project timeline can be devastating.
According to a recent study by BluePrint Supply Chain in partnership with Data Center Frontier, 64% of industry professionals have identified missing or damaged mission-critical gear as having an extensive or moderate impact on their project budget. This insight highlights the critical importance of a reliable quality assurance (QA) program and consistent reporting across the entire construction supply chain to safeguard the condition and operational integrity of your gear.
Quality Assurance and The Chain of Custody
To effectively implement a quality assurance program, we must look at every link in the chain of custody of mission critical gear. Essential components and equipment must be confirmed for arrival, physically inspected, and their condition documented at every touchpoint in their journey. Each stakeholder in the chain, whether it’s the manufacturer, transportation provider, warehouse location, or crane and rigging company, must be held accountable for your gear while it is in their custody.
Manufacturer:
Most manufacturers for mission critical gear in the data center space have some type of warranty or guarantee on their products from the time they leave the manufacturer’s floor or warehouse to the time they arrive at the buyer’s location. However, some manufacturers end their warranty upon pick up—or have conditional warranties based on certain preferred logistics supplier and transportation companies—it is important to understand the policies of the OEM or supplier prior to shipping the gear.
At this point in the chain gear is generally considered to be in excellent condition and should be documented as such by the manufacturer.
First Mile Haul:
Generally, this is the first opportunity for damage to occur. While service providers can’t eliminate risk, they can certainly mitigate threatening circumstances through clear communication, planning, and preparation.
Prior to pick up, make certain the chosen transportation or logistics firm has the proper equipment and experience to do the job. Work with the manufacturer to ensure equipment specifications, crating and loading plans are reviewed and understood by the supplier. Take note of any special sensitivities the equipment may have—such as aversion to moisture, extreme heat or cold, or excessive vibration and make certain that your transportation company has taken steps to account for these special handling instructions.
It is also important, especially when dealing with oversize/overweight loads, that routes are planned well ahead of time and that all relevant permits and licenses have been obtained and filed. While not necessary, it is also a good idea to work with a company that provides some level of GPS tracking to monitor the location of your gear while in transit.
The condition of the equipment should be inspected and documented at the beginning of the journey after it has been loaded onto the truck then again upon arrival at its final destination.
Warehouse/Integration Site:
For data center projects, mission-critical equipment is often stored and sometimes pre-assembled at the warehouse or integration site. Quality assurance is essential to prevent damage or loss. Each item should be inspected and documented upon arrival, with regular inventory checks to track its status and condition. Serial numbers as well as any other identifying information should be verified and recorded as well. Make sure that the warehouse vendor is double-checking the numbers with the manufacturer, so no mistakes are made at intake into their inventory management system.
An effective inventory management system streamlines this process, providing real-time visibility into stock levels and ensuring that items are readily available when needed. Proper sequencing during storage is critical; equipment and components needed first should be placed in accessible locations, ensuring that retrieval is efficient and minimizing delays. This system not only enhances operational efficiency but also supports accountability throughout the supply chain.
The warehouse is designed to keep everything secure and ready for the next steps. Clear communication with suppliers and partners ensures all items are accounted for and in good condition before final transport to the job site.
Last Mile Haul:
The last mile haul is a crucial phase in the supply chain, as equipment moves from storage to its final destination. To mitigate risks during this stage, a final inspection of each item should be performed, documenting any changes in condition since its arrival at the warehouse, prior to loading. Just like the first-mile journey, collaborating with logistics partners to plan the route is essential to ensure all necessary permits are secured and special considerations—such as handling oversized loads or fragile equipment—are addressed. Implementing tracking solutions, such as GPS monitoring, provides real-time updates on the equipment’s location. These precautions ensure the gear remains in good condition until it reaches the job site and its location is readily visible.
Jobsite:
When mission-critical gear arrives at the job site, it is essential to conduct a comprehensive inspection to confirm that everything is intact and meets project specifications. Proper storage and handling protocols should be followed to protect equipment from potential damage during the construction process. Clear communication among project managers, installation crews, and logistics teams is vital to ensure smooth operations and facilitate timely integration into the workflow. By maintaining strict quality assurance measures, teams can swiftly address any issues that arise, helping to keep the project on schedule and aligned with the expected outcomes.
Reporting
You want to ensure a comprehensive reporting process that captures the status of mission-critical gear throughout the entire project lifecycle. Each stage of the supply chain must be clearly documented, providing a straightforward record of inventory levels, condition assessments, and inspection outcomes.
Consistent reporting promotes accountability among all stakeholders and allows for quick identification and resolution of potential issues before they escalate. Establish clear key performance indicators (KPIs) to gauge the effectiveness of your quality assurance efforts, focusing on metrics such as on-time delivery, condition upon arrival, and their impact on project timelines and budgets.
Prioritizing effective reporting practices enhances collaboration among teams and protects the integrity of your valuable equipment, ultimately contributing to the successful execution of your data center projects.
The Long-Term Value of Quality Assurance
Investing in quality assurance is a strategic move that yields long-term benefits for supply chain efficiency. Companies that proactively implement QA measures are better positioned to minimize costly delays and foster trust with clients. Our research with Data Center Frontier illustrates the significant impact that issues related to lost or damaged materials can have, highlighting the need for effective quality assurance to mitigate risks and ensure smoother operations. As data center projects become increasingly complex, the importance of effective QA becomes even clearer. By carefully managing materials throughout the supply chain, companies can support seamless project execution and enhance overall performance.
Quality assurance reporting also establishes a foundation for continuous improvement. Building strong relationships with top-performing vendors becomes increasingly beneficial as key performance indicators (KPIs) such as efficiency and total cost of ownership (TCO) improve. By prioritizing quality assurance, companies not only enhance project outcomes but also secure long-term success in the competitive data center landscape.
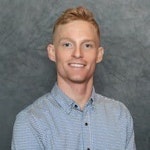
Joey Wagner
Joey Wagner, a Program Management Subject Matter Expert at BluePrint Supply Chain, is known for applying his expertise in business development and operational strategy to drive innovative and efficient supply chain solutions for the data center industry.
BluePrint Supply Chain manages logistics, storage, and installation of mission-critical equipment for industrial construction projects. Their P2M™ method—Plan, Manage, Measure—provides tailored logistics solutions that enhance operational efficiency and drive competitive success. Learn more at BluePrint Supply Chain.