Understanding PFAS Concerns for Two-Phase Cooling of Data Centers
Data center cooling accounts for approximately 1.2% of global electricity use, or about the same amount needed to power over 19 million homes. And with liquid cooling using roughly half the energy of air cooling, it’s become the logical choice for many operators, especially as chip densities inch upwards to a point that air can’t handle. Within the liquid cooling landscape (immersion vs. direct-to-chip and single vs two-phase) we’ve seen two-phase, direct-to-chip receive growing attention given its high reliability and superior ability to cool high-power chips.
From a sustainability perspective, stakeholders must worry not only about energy and water consumption but also global warming and human health issues. As it relates to the latter two, the most pressing issues are related to the use of the two-phase working fluids employed in these systems, similar to the sustainability issues surrounding refrigeration and HVAC equipment. Most, if not all, two-phase cooling solutions for data centers currently use refrigerants that fall under the category of per- and polyfluoroalkyl substances (PFAS). The sustainability related concerns associated with PFAS have only been amplified by the European Union’s recent string of proposed legislative actions to regulate or ban PFAS, the so called “forever chemicals”. What are PFAS? And should prospective data center two-phase cooling stakeholders (including investors, data center operators, server manufacturers, integrators, and others) be concerned about the sustainability of PFAS refrigerants in two-phase cooling systems?
Should all PFAS be considered “Forever Chemicals”?
First, we must understand that the family of chemicals that PFAS covers is diverse. The umbrella of chemicals covered by PFAS is not unlike hydrocarbons. Hydrocarbons cover anything from natural gas to gasoline to mineral oil to candle wax to plastics; even though they all consist of essentially the same atoms, the properties of and applications for hydrocarbons vary widely. The main chemical feature that distinguishes these seemingly diverse subgroups of chemicals is the size of the molecules (larger molecules tend to be more solid, smaller molecules tend to be gaseous, and liquids fall in between). Similarly, PFAS can be in vapor or liquid form (refrigerants) or in solid form (plastics or plastic coatings, such as polytetrafluorethylene [PTFE]). The distinguishing feature of PFAS is the presence of one or more fluorine atoms attached to the carbon backbone of the substance’s molecular structure. Adding fluorine to a molecule tends to offer performance benefits, including lower chemical reactivity, lower flammability, lower toxicity, lower friction, etc., so fluorinated chemicals have seen use across many everyday applications.
The “forever” nature of PFAS depends largely on their lifecycle as they escape into the environment. Figure 1 shows a diagram of the lifecycle of high molecular weight, solid PFAS. After being produced in a factory and integrated into common items such as coatings and fabrics, the solid PFAS are ultimately discarded once the items end their useful life. Since these PFAS are solid, and inherently long lasting (chemically non-reactive thanks to the fluorine!), they tend to find their way into soil and ground water and eventually into the water table as they breakdown down into small particles. Once in the water table, the particles are ultimately consumed by organisms such as fish and humans (directly through water or through the fish!). Again, the pervasive nature of PFAS causes them to reside in these organisms, since they do not break down chemically. Further, organisms typically do not have natural ways to expel these particles once consumed.
Fortunately, lower molecular weight liquid or gaseous PFAS (such as those used in HVAC, refrigeration, and data center two-phase cooling systems) take a different life cycle (See Figure 2). In the event of a leak, the PFAS refrigerants vaporize and eventually make their way into the upper atmosphere. In the upper atmosphere, two things can happen based on the global warming potential (GWP) of the vaporized PFAS refrigerant.
- For PFAS with high GWP, the PFAS remains in the upper atmosphere, where it has a high potential to warm the globe (not shown in Figure 2)
- For PFAS with low GWP, the PFAS substance breaks down in a matter of days into the naturally occurring compound triflouroacetic acid (TFA)
Low GWP PFAS refrigerants quickly breakdown into TFA in the upper atmosphere due to the presence of UV radiation. Fortunately, TFA is a naturally occurring compound and, if consumed, can be excreted by organisms like most salts and ions. It should also be noted that many liquid and gaseous PFAS, regardless of their GWP, are routinely recycled at end-of-life, which eliminates any risk of environmental release or harm.
What are the specific concerns regarding PFAS in two-phase cooling systems?
Although some two-phase cooling vendors stubbornly use refrigerants with high GWP, most vendors offer options that have low GWP. Accelsius’ Neucool platform exclusively features low GWP refrigerants. Low GWP refrigerants include R1233zd(E), R1336mzz(Z), and R1234yf amongst others. These refrigerants belong to a class of chemicals called hydrofluoroolefins (HFOs) and hydrochlorofluoroolefins (HCFOs). HFOs and HCFOs have been developed and commercialized specifically to replace older refrigerants, including hydrofluorocarbons (HFCs) and chlorofluorocarbons (CFCs) that were phased out due to their higher global warming and ozone depletion potentials. HFOs and HFCOs, by contrast, have inherently low GWPs (typically around 1) and low ozone depletion potentials (near zero) compared to HFCs which have high GWPs (around 1,000) and CFCs which have much higher GWPs (between 5,000 and 15,000) and higher ozone depletion potentials (above 1.0).
Chemical manufacturers have shared that HFOs are currently used as blowing agents to manufacture everyday building products, such as polystyrene foam. In fact, in the process to manufacture extruded polystyrene foam, HFO blowing agents are vented into the atmosphere with no negative environmental impact. While these manufacturers have not provided firm positions on future regulatory concerns related to HFOs, their expansion plans suggest confidence in ongoing regulatory acceptance of HFOs as low GWP and low ozone depletion potential compounds compared to other refrigerants.
Do all two-phase cooling technologies release the same amount of refrigerant into the atmosphere?
In practice, direct-to-chip two-phase cooling companies (such as Accelsius) and their customers will use standard refrigeration industry practices to store and dispense these refrigerants, as is done every day in the HVAC industry worldwide. Industry-standard practices include using sealed storage tanks, leak-free quick disconnect fittings to dispense and transfer refrigerants, and sealed operating systems that are regularly checked for leaks. Release of the HFO and HFCO refrigerants is never expected, but, in the event of a leak, any refrigerant that is released will vent as a gas and proceed through the low GWP life cycle previously presented in Figure 2. At end of life, the systems are designed such that the refrigerant can be completely evacuated into a vessel provided by the chemical manufacturers and returned for recycling.
The same cannot be said of two-phase immersion cooling based approaches. Every time an immersion bath is opened for maintenance or otherwise, large amounts of PFAS can quickly evaporate into the data center and eventually the atmosphere. Further, the amount of refrigerant present per rack is typically 20 to 30 times more than is present in any direct-to-chip two-phase cooling rack. That being said, the refrigerants used are similar in nature to those used by direct-to-chip, and similar life cycles and recycling policies are expected to be followed.
Summary
Recently, the data center industry has increasingly turned toward liquid cooling for its energy efficiency benefits. The particularly strong interest in two-phase, direct-to-chip cooling directly results from its exceptional ability to handle the most intense heat loads from high-power chips, along with its superior reliability when compared to other liquid cooling methods. However, there is often a moment of pause when people consider the use of PFAS refrigerants in two-phase solutions, due to a lack of understanding about the PFAS that are truly “forever” and the PFAS that are truly “not forever”.
We want the industry to understand the nuances in the PFAS story so that users can make informed choices about how to save energy while also protecting the environment. To reiterate, there are several two-phase refrigerant options that have an inherently favorable life cycle which delivers low GWP and, in the event of a leak, naturally degrade to benign compounds.
Accelsius was founded to deliver both economic value and sustainability benefits with its thermal management solutions. We have been thoughtful in choosing HFO and HFCO refrigerants that are safe, have a GWP at or near 1, and do not contain the kinds of “forever” PFAS that persist in the environment. We also engineer our thermal management systems to use as little refrigerant as possible; we currently require about 1/30th the amount of refrigerant used in immersion solutions.
We will continue to monitor coolant regulations and technical development to ensure that Accelsius is always at the forefront of delivering the most sustainable cooling solutions – in terms of energy, water use and environmental impacts.
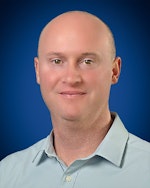
Richard Bonner
Richard Bonner is Chief Technology Officer at Accelsius. Dr. Bonner has over 18 years of industrial experience as a heat transfer researcher and advanced thermal product developer. He is a recognized expert in two-phase cooling and thermal issues as they relate to the energy-water nexus, authoring over 50 papers and 5 issued U.S. patents. Dr. Bonner holds a B.S., M.S., and Ph.D. in Chemical Engineering from Lehigh University.
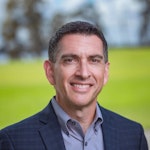
Bill Grieco
Bill Grieco is Chief Technology Officer at Innventure. Bill is an entrepreneur, innovator, and business leader who has spent the last 25 years leading R&D and commercialization organizations in the chemical, pharmaceutical, clean tech, and specialty materials industries. He holds chemical engineering degrees – a PhD and Master’s degree from M.I.T., and a Bachelor’s degree from Georgia Tech.
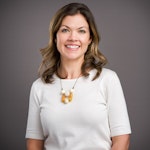
Liz Cruz
Liz Cruz is Director of Product Management at Accelsius. Liz has 15+ years’ experience in the data center sector, spanning roles across research, sustainability, events & media and most recently on the solution provider side, working to solve power & cooling issues in the data center. She holds an MBA and BA from the University of Texas at Austin.