How Technology Can Transform Data Center Construction
PHOENIX, Ariz. – The construction site of the future may look very different. Data centers will be pieced together from pre-fab components built in factories, with on-site teams assembling walls, components and sometimes entire rooms. Teams are guided by 3D modeling applications offering virtual reality “walk-throughs” of projects in progress, with custom views for architects, executives and engineers. Meanwhile, experienced workers and women use exoskeletons to hoist power tools for long shifts alongside younger and stronger colleagues.
“The future of construction is technology driven,” said Nancy Novak, Senior Vice President of Construction at Compass Datacenters. “Some of these technologies will help alleviate labor challenges.”
In a presentation at Data Center World, Novak reviewed several technologies that offer ways to make construction faster, cheaper, safer and more efficient. She made the case that embracing these tools to make construction more agile is no longer an option, but now a necessary step if the data center industry is to keep pace with the global boom in cloud computing. It’s a huge challenge, complicated by a shortage of skilled construction workers.
“It’s an unprecedented feast for construction,” said Novak. “There’s more work than anyone can possibly do. We need to do more with less. If we don’t change things now, when will we?”
That change must extend to creating opportunities for women in construction, said Novak, who has been a vocal advocate for making the trades more inclusive. Training and hiring more women can be a key solution to the many challenges facing construction, she said, and technology can be an important enabler of this trend.
Pre-Fab and Off-Site Manufacturing
Novak speaks from more than 25 years of leadership in the construction industry, including a variety of executive positions at Balfour Beatty Construction and Hensel Phelps prior to joining Compass in 2017.
At Data Center World, she noted that change often arrives slowly in both the construction and data center industries. One example is the adoption of off-site construction using pre-fabricated components built in factories. Modular techniques have become common in some industries, most notably in hotels, offices and student housing.
Nancy Novak, Compass Datacenters.
“We’ve been toying around with this for several decades, and yet it’s still an anomaly,” said Novak, who noted that Compass makes extensive use of off-site construction in its standard design, using pre-fabricated components to control cost and the delivery timetable. To speed construction, the entire building is precast, allowing Compass to go from foundation to a completed building framework in 18 to 21 days. Each power room is pre-fabricated, and then attached to the building.
The data center industry has been using some form of modular design since 2006, when Sun Microsystems’ unveiled its “Black Box” container to house servers. The concept was refined in cloud data centers for Microsoft (even for underwater deployments), while IO and its BaseLayer unit developed IT modules for colocation and enterprise use. Data center developers like Compass, CyrusOne and Digital Realty have used pre-fab power and cooling infrastructure to accelerate construction, and pre-fab construction is also being used to deploy cable landing stations for subsea cables.
But Novak sees plenty of room for off-site construction to accelerate the delivery of data center capacity.
“A data center is unique, because it’s all driven by power and air,” said Novak. “Seventy-five percent of the labor is in the MEP (mechanical, electrical and plumbing), not the real estate. So if you really want to save money, you have to get your MEP to offsite manufacturing.”
Pre-fabricated construction can be used to create components like duct banks or elevator shafts or bathrooms, or for entire power rooms. Demand for off-site data center construction is likely to accelerate as more companies pursue multi-story vertical construction and distributed edge micro data centers – a niche Compass is targeting with its EdgePoint offering.
What can be done off-site? Novak says a better starting point is to ask what CAN’T be done elsewhere. “Start there, and do everything else offsite,” she said.
Off-site techniques move the data center industry closer to a “just in time” delivery system, but there’s often tension around the timing of when manufacturing can commence. “A lot of this is about business models, and putting the cart before the horse,” said Novak. “It’s always this ebb and flow (between order and product).”
Many companies now provide off-site manufacturing and fabrication for industrial construction, including data centers. But not all are created equal, and that matters when project timelines are tight. “The companies that are ‘in it to win it’ are investing hugely and retooling to stay current,” she said.
Novak says off-site construction is important in creating a more diverse construction labor force, which will help meet the staffing challenges.
“Continuing to take labor off the job site allows us to be more inclusive,” said Novak. “It’s hard to always work on a remote job site. When you’re the primary caregiver, which most women are, it’s hard to make that one- or two-hour drive and drop kids off (at daycare or school) beforehand. Nobody opens that early.
“Off-site construction offers a controlled environment and 9-to-5 workdays,” said Novak. “This is a great opportunity for women to get into the trades. And it’s hard to find skilled tradespeople.”
PAR, VR and the Power of Software
The adoption of artificial intelligence is a major factor in the growth of the data center business, as technology companies use adopt AI to create smarter apps and services. “AI is going to drive the need for data center capacity,” said Novak.
AI can also enhance tools for managing construction. That’s particularly true with tying together data streams from the many disciplines involved in building a data center, including architects, construction executives and MEP engineers. Modeling programs can help teams work together to design and build a project, often aided by 3D virtual reality visualizations.
“The inter-disciplinary translation issue is a consistent challenge,” said Novak. “Software should solve this. That’s where the future will take us.”
Another challenge is complying with local construction codes that vary across the country. This is the kind of data challenge where AI can bring order out of chaos.
“The thing that’s going to be really disruptive is all the data that’s stored, but not organized,” said Novak. “That’s where AI will help us. We can’t even see five years down the road. We don’t know what AI’s going to look like in the future.”
Robotics and Exoskeletons as Workforce Enablers
Novak got the room’s attention with a video displaying exoskeleton technology from Ekso Bionics, which makes robotic exoskeletons that support workers, allowing them to lift heavy tools and components.
The EksoVest exoskeletons, which are used at Ford Motor Company factories and many construction job sites, can help reduce injuries, and allow older workers to be more productive and work longer hours. “The experienced talent is getting old, and it’s hard on their bodies,” said Novak.
Exoskeletons could also open construction jobs to more women, who typically have less muscle mass than men. “Think what this would do for our industry,” she said. “I think of this as a wonderful advancement. It needs to become affordable.”
Novak acknowledged that robotics can be a hard sell, due to anxiety about new technology (a fear fed by decades of science fiction movies).
“We’re struggling to get resources, and robots still scare us,” she said. “This is an opportunity for growth. It’s nothing to fear. You don’t have to like it, or agree with it, but it’s not going to stop. This is where this has to go. These technologies are coming, and coming fast.”
Recapturing the Nobility of the Trades
Technology can play an important role in addressing the labor shortage and making construction more inclusive for women. But it must be accompanied by a cultural shift, which the construction sector must lead.
Parents are steering young people away from trades and construction, prioritizing technology skills over “digging a ditch” and other manual labor.
“There’s a huge incentive for us to change that image,” said Novak. “It takes time. We’re hoping the new technologies will attract millennials to use their skills to innovate.”
“We need to bring back the nobility of what a skilled trades person does,” said Novak. “We’re already depleted. We’ve waited a long time to figure this out, and now we’re there.”
Ultimately, bringing change to data center construction will require a combination of new technology and new thinking.
“Innovation comes through a combination of new ideas,” said Novak. “It’s hard to have a different set of lenses. Our clients have gotten there. Our industry has not.”
About the Author
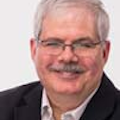