We continue the Data Center Executive Roundtable for Fall 2015 with a discussion of the development of modular data center designs and factory-built components. Our panel of four experienced data center executives – Chris Crosby of Compass Datacenters, Rob McClary of FORTRUST, Douglas Adams of RagingWire Data Centers, and Harold Simmons of United Metal Products – notes that definitions and language still loom large in the discussion of pre-fabrication.
The Role of Pre-Fabricated Designs
Data Center Frontier: Factory-built components are playing a larger role in data center deployment. What’s your take on the impact of pre-fabrication in data center construction, and its role in the future of the industry?
Robert McClary, FORTRUST
Robert McClary: Building a data center is a huge capital investment. Anything you can do to reduce the costs, including pre-fabrication and/or modular design, and better allocating capital in a just-in-time type model, makes perfect sense. It is hard to increase the quality of a data center’s infrastructure and reduce cost if every data center has a substantially different design than the last.
Pre-fabrication in the data center market has been slow to evolve, in part due to the fact that engineers want to keep designing data centers and re-purposing specifications within the same paradigm they’ve had for the last 20 years, with only slight modifications.
Pre-fabrication is starting to catch on because of the undisputable economic advantages. More data center owners should be demanding that their engineering and general contractor firms look at pre-fabricated or modular models.
Chris Crosby: This is a good question that is muddied by the lack of clarity in definition. At Compass, for example, components like our PowerCenters are built off-site and shipped to the location for installation. The walls of our facilities are pre-fabricated, structural pre-cast and then erected on site. So if we are defining pre-fabricated from this perspective, I would say that it’s making very positive impact on the industry and will continue to become more pervasive in the future.
Chris Crosby, CEO, Compass Datacenters
If we were defining “pre-fabricated” as shipping container-like structures that are built in “factories” and then shipped to site then my answer would be totally different. These PFM modules are niche plays that make a lot of sense in the right application environments. In and of themselves, they are simply not capable of providing the mission critical level of application support that enterprises require. For example, no one would put a $10 million IBM mainframe into a container in the middle of the parking lot. First off, the mainframe’s footprint doesn’t work. Secondly, I would not want to be the guy who has to explain to my executive team why this was a good idea when something goes wrong.
Obviously, there are hardened PFMs, but those are for the right applications. Third-world, harsh environments tend to be the best suited for these approaches.
Most PFM have to be housed somewhere, thereby requiring the end user to either build a hardened shell or have a suitable building available. Due to the nature of their construction – a 12-foot by 40-foot footprint for example – they don’t lend themselves to delivering a flexible environment that can easily be adapted to changing requirements, since floor space must be configured in typically less than 1,000 square foot increments and all load groups must be homogenous. This doesn’t mean that they aren’t well suited for very defined applications, but I don’t see them ever becoming a major element of the data center marketplace.[clickToTweet tweet=”Harold Simmons: Pre-fabricated components will play a key part in data center deployment.” quote=”Harold Simmons: Pre-fabricated components will play a key part in data center deployment.”]
If you don’t believe me, look at Google and Microsoft. Google no longer uses containers (not since mid to late 2000s), and Microsoft just replaces the whole container when a certain amount of servers go bad. It’s hard to believe that those guys haven’t figured out that Move-Add-Change in metal boxes is really inefficient.
Douglas Adams, RagingWire Datacenters
Douglas Adams: The notion of containerized data centers is all but dead, except for single tenant facilities and some small outlying use cases.
What is working in the data center market is modularization. Driving the complexity and cost into the supplier’s hands and abandoning the old days of assembling and programing equipment in place is key to any data center provider offering a high-quality, affordable offering.
Again, this is a case where scale is very important, as only at-scale providers can effectively push these costs up-stream to their equipment providers.
Harold Simmons, United Metal Products
Harold Simmons: Pre-fabricated components will continue to play a key part in data center deployment. Pre-fabrication has allowed the lead time required for new data centers to be built to be significantly reduced.
Overall, factory built components also offer the opportunity for greater quality control, tax depreciation advantages, and improved construction schedules.
While it does not look like pre-fabricated solutions will completely eliminate traditional brick and mortar facilities, it has become apparent that a hybrid approach to infrastructure build offers key advantages over simply locking in on one methodology.
NEXT: Our panel discusses the innovation landscape in data center cooling.
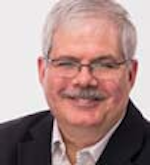