Evaluating CDU Expansion Tank Technology: What Are the Most Important Factors?
Coolant distribution units (CDUs) play a critical role in the liquid cooling systems used in data centers. CDUs manage and distribute coolant to maintain optimal temperatures for high-density computing environments. They ensure the coolant is delivered at the right temperature, pressure and flow rate while creating an isolated secondary loop separate from the primary chilled water supply. This helps precisely control the cooling system, prevent condensation, and facilitate efficient heat removal. By employing liquid, which is more effective than air at transferring heat, CDUs enable data center cooling systems to handle higher heat loads, making them an ideal technology for modern data centers running high-powered CPUs and GPUs.
While CDUs are instrumental in cooling IT equipment, they also present their own set of challenges. The secondary loop in CDUs is susceptible to varying liquid temperature changes as the liquid circulates through the system. These temperature changes cause the liquid to expand and contract, putting stress on mechanical components. CDUs need to dynamically respond to these liquid temperature changes without causing any plumbing failures in the system. To address this challenge, CDUs are equipped with an expansion tank, a crucial component that helps manage these temperature-induced liquid expansions and contractions.
Generally, expansion tanks are divided into two types: standard expansion tanks and flow-through tanks. Both types provide space for the liquid to expand in a cooling loop, but they do so in different ways.
Standard expansion tanks have their inlets and outlets in the same location. Standard expansion tanks include several sub-types, including open tanks, closed tanks with no bladder, and closed tanks with a bladder. As the name suggests, open tanks are open to the atmosphere. These designs are not used in CDU systems because they disrupt the closed-loop design. Closed tanks (with or without a bladder) have no openings to the atmosphere, but adding a bladder can modulate the liquid volume inside the tank as required.
Another factor to consider is that, unlike conventional expansion tanks in other industries, CDUs also use their expansion tanks as reservoirs, adding a layer of complexity to their operation. During normal operating conditions, the tank contains a certain amount of liquid inside, which is used as a backup source when the system loses volume during filter replacement.
An advantage of standard expansion tanks are their small and compact size. However, standard expansion tanks present challenges for liquid circulation inside the tank, especially since CDUs also use expansion tanks as reservoirs. Liquid brought into the tank during operation may or may not regularly circulate back into the system loop. This stagnant water increases the potential for microbial growth inside the tank, underscoring the need for innovative solutions. Even though various systems employ PG25 to avoid this, de-ionized water is also a widely used coolant in the industry. The ideal growth range for one of the primary bacterial types is between 20° and 40°C—right in the operating range of a typical CDU.
Due to this concern, some standard tanks come with a mixing device, usually installed at the tongue of the tank. This mixing device helps circulate the liquid inside the tank by creating high and low pressure regions. However, the performance of these mixing devices varies based on their design, and the water's circulation time heavily depends on the flow rate.
Flow through expansion tanks can provide another answer to this challenge. As the name suggests, flow-through expansion tanks have inlet and outlet connections at opposite ends. These tanks are installed in line with the liquid loop, where the liquid constantly circulates through the tank during regular operation. During thermal expansion, the inner volume expands radially but maintains its flow-through characteristics. The flow-through characteristics and the size of the inlet/outlet openings often create turbulence within the tank, which further mixes the liquid. This design dramatically reduces the chances of microbial growth in CDU loops, making flow-through expansion tanks an excellent choice for the future of the data center industry.
Bacterial growth in CDU liquid can create serious challenges that may require isolating the whole system for maintenance, thereby shutting down the mission-critical IT equipment. Thinking through expansion tank design to reduce bacterial growth inside the hydraulic loop of the CDU is just one piece of the puzzle, but it is vital to elongate the life and improve the reliability of CDU systems. Equipping a data center with the right CDUs to power next-generation AI chips is critical to the functioning of data centers.
About the Author
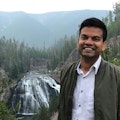