Best Practices for Deploying Liquid Cooled Servers in Your Data Center
With the surge in demand for AI and high-density server systems, data center operators are now more than ever considering liquid cooling. But how can operators ensure direct liquid cooled (DLC) systems are designed, deployed and maintained to industry standards? Here are the best practices recommended by CoolIT Systems, the global leader in liquid cooling.
Who is involved?
DLC deployments will have three main stakeholders:
- Data center operator (DC operator)
- Server manufacturer or system integrator (OEM/SI)
- Direct liquid cooling vendor (DLC vendor)
Close collaboration between the DC operator, OEM/SI, and DLC vendor is essential for success in each DLC implementation phase, which includes design, deployment, and maintenance.
Phase 1: Design
The DC operator starts the design phase by developing system requirements by working with an OEM/SI to determine the optimal liquid-cooled IT solution based on rack locations, facility infrastructure, and performance needs. Once system-level requirements are established, the DC operator and OEM/SI can develop specific liquid cooling requirements in collaboration with a DLC vendor, who should provide a comprehensive intake questionnaire and perform an on-site visit. The DLC vendor will size the system and design the liquid cooling solution. This includes selecting the coolant distribution unit (CDU) model, the number of CDUs, and secondary fluid network (SFN) routing. The DLC vendor also provides guidance to the DC operator and OEM/SI on facility requirements and the deployment’s scope of work.
Phase 2: Deployment
Once the DC operator has selected the server systems and the liquid cooling solution, the DLC vendor and OEM/SI work on logistics, product delivery, and system scheduling. The DLC vendor works directly with the DC operator for facility coordination on SFN and facility piping designs. If required, the DLC vendor engages a local Authorized Service Provider (ASP) to assist in installing and maintaining the liquid cooling system.
During the installation, the DLC vendor installs the liquid cooling equipment necessary to route the cooling medium from the CDU directly to the DLC servers. After a post-install validation process is complete, the DLC vendor proceeds to start up the liquid cooling system. Commissioning of the system is finalized by full performance testing and tuning done in collaboration with the DC operator and OEM/SI. This includes flow balance testing, pump tuning, and thermal load testing.
Once the installation and testing are complete, the DLC vendor officially hands over to the DC operator.
Phase 3: Maintenance
Routine maintenance is the final stage in a successful DLC deployment. A DC operator can commission the DLC vendor and its ASPs to perform regular maintenance based on the planned preventative maintenance (PPM) schedule, which should occur at least every six months. In the event of an issue or unscheduled repairs, onsite break-fix support and 24/7 global response support should also be incorporated as part of the maintenance coverage.
Conclusion
The successful deployment and operation of direct liquid cooling (DLC) systems in data centers hinge on the close collaboration between the DC operator, OEM/SI and DLC vendor. Each phase – design, deployment, and maintenance – requires meticulous planning and coordination to ensure that the DLC systems meet industry standards and deliver optimal performance. By adhering to best practices and leveraging the expertise of all stakeholders, data centers can effectively harness the benefits of liquid cooling, thereby meeting the demands of high-density server systems while maintaining efficiency and reliability.
About the Author
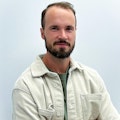
Chad Brears
Chad Brears is a Manager of Project Engineering at CoolIT Systems, helping to lead a globally driven group of project engineers that are focused on technical solution design and deployment of CoolIT’s liquid cooling products.
CoolIT Systems specializes in scalable liquid cooling solutions for the world’s most demanding computing environments, partnering with global processor and server design leaders to develop the most efficient and reliable liquid cooling solutions for their leading-edge products. Click here to learn more about CoolIT’s end-to-end product portfolio.