Beyond the Generator: Secrets to Finding the Perfect Data Center Backup Power Enclosures
Ensuring a reliable and resilient data center goes beyond just picking a generator. An often overlooked, yet crucial element of your backup power system is the generator enclosure. While the generator itself might seem like the star of the show, the enclosure plays a critical role in how well it performs, how safe it is, and how easy it is to maintain. For data center leaders, it’s important to understand lesser-known factors surrounding generator enclosures. Understanding these details will empower you to make informed decisions for your data center and ensure your backup power solution is configured exactly to site specifications.
The Often-forgotten Backup Power Hero: The Generator Enclosure
Most generator manufacturers offer fairly standard products. As a data center manager, it's easy to assume that choosing a powerful generator is the main step in securing reliable backup power. But there's more to the story. While the generator itself may be straightforward, finding the optimal enclosure for it can be the real challenge.
Unlike many standardized data center components, each facility's environment presents unique challenges. To find the perfect backup power solution, you need to consider factors like noise restrictions, temperature needs, and available space. For many, integrating the generator into a suitable enclosure is a critical decision point and a true test of how well a vendor can meet your specific needs.
What Separates a Good Enclosure Setup from a Great One?
You may know the main things to look for in an enclosure—the air intake, the entranceways, the fuel system—however there are other, lesser-known elements that sometimes go overlooked. Beyond the essential factors to consider, the often unnoticed aspects can significantly impact the performance, maintenance, and lifespan of your backup power investment. Here are some of the more nuanced, yet still essential details you should consider.
First: exhaust configuration matters. Often, a data center's building design is finalized before backup power is considered. This means the enclosure footprint needs to be flexible to accommodate existing constraints, which frequently means designing the exhaust setup is relegated to being an afterthought. Improper exhaust flow, though, can have serious consequences. In the worst-case scenario, hot engine air can be directed into the space where the data center's chiller plant draws air, compromising the entire facility’s cooling system performance. To prevent future problems, exhaust systems need to be carefully considered in the context of the facility layout. This might involve strategically placing the exhaust during the initial site design phase, or getting creative with exhaust stack size and direction after the fact using custom-fabricated components.
Another regularly unnoted element of evaluating an enclosure is the small details around rust prevention. Like any long-term hardware investment, protecting your enclosure from rust is vital. Most enclosures are made from aluminum to prevent corrosion, but external fasteners can become weak points over time. A rusty bolt or rivet head can lead to rust streaks that compromise the integrity of the enclosure panels over the years. The ultimate solution is to eliminate external fasteners in the first place: using adhesive skin as a sealed, overlapping material over the enclosure panels removes the need for rivets or bolts — eliminating the possibility of rust altogether.
Relatedly, corrosion can also affect noise-reduction equipment. Some silencers are mounted externally on the enclosure roof. Since silencers are typically made from painted steel, they're susceptible to rust, especially since high exhaust temperatures can damage any protective paint. Internal silencers offer a solution here, as they are located within the enclosure and thus protected from the elements.
Flexibility is Key
Above all, finding the right enclosure involves working with a manufacturer who offers a collaborative and productive design process. When engaging in such a process, there are two main approaches to meeting your specific requirements. One is where your data center team might have pre-determined specifications for pre-engineered components and a preferred layout for the enclosure. In this situation, you can bring these specifications to the vendor and then collaborate on how to best approach the desired elements. Another approach is to depend on vendor expertise to guide you. In this lane, if your team doesn't have specific ideas for enclosure construction, you can work closely with the vendor to develop specifications that meet all your site constraints.
Regardless of which approach you choose, an effective method for developing and agreeing on project specifications is crucial for a successful outcome. So, when shopping for an enclosure, make sure you’re asking questions about the process, and not just the product:
- Will I have a dedicated point of contact?
- Do you offer a variety of pre-engineered components that can be mixed and matched to meet our unique needs?
- Can we collaborate virtually on the design process?
- How can we work together to streamline the installation process on-site?
These can be important conversations not just for potentially buying a backup power solution, but to see if your vendor is the right fit for your needs.
It's What’s on the Outside That Matters
As a data center, it's easy to believe that selecting a power node is the primary step in securing the right backup power solution. However, while choosing a generator might be straightforward, finding the ideal enclosure for it can be the true challenge. By paying extra attention to consider some often-overlooked factors, you can ensure you choose a generator enclosure that perfectly meets your data center's needs and keeps your data center’s backup power system running smoothly for years to come.
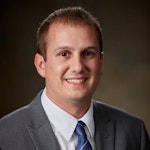
Justin Loritz
With over 17 years at Kohler, Justin Loritz is a seasoned expert in diesel engine product management and manufacturing systems. As the current Product Manager for large diesel products, he leads advancements in high-performance power solutions for data centers and other industries. His previous roles include Principal Engineer in Manufacturing Systems, where he optimized production processes, and Cell Manager for Highly Engineered Assembly, overseeing complex assembly operations. Holding a BS in Mechanical Engineering from Michigan Technological University, Lortiz combines deep technical knowledge with practical industry insights, making him a recognized authority in mission critical backup power systems.