Unpacking CDU Motors: It’s Not Just About Redundancy
Liquid cooling is here. Next-generation chips and other AI infrastructure need more efficient cooling methods to keep them from overheating. Today, many data centers implement solutions that remove extra heat by increasing air volume or reducing air inlet temperatures, which can be inefficient and costly to run. When air cooling systems have to work harder to maintain optimal temperatures, facilities can also face equipment breakdowns, unexpected shutdowns and increased energy costs.
For many data centers, using liquid cooling technologies can offer better performance while reducing energy use and helping data centers operate more efficiently. For the most advanced applications, liquid cooling is the only possible option. By using liquid cooling technologies in the right way, data center managers can greatly improve Power Usage Effectiveness (PUE), even in applications where they are using next-generation IT.
A critical part of any liquid cooling system is the coolant distribution unit, or CDU. The CDU acts as the “heart” of the liquid cooling system, pumping cooled fluid through racks at an appropriate rate for the cooling needs of the system. CDUs need to dynamically respond to the cooling needs of IT by changing the rate at which fluid flows through the system. However, there are a few methods of controlling CDU pumps. Each method has benefits and drawbacks.
Powering The Data Center’s Heart
There are two main types of drives used in CDU pump motors: variable speed drives (VSDs) and variable frequency drives (VFDs). Both adjust the speed that motors run to respond to the cooling demands of IT systems, circulating liquid through the system at different rates. However, there is a key difference between them. VSDs manage motor velocity using amperage and voltage, supplying less net input voltage when the motor doesn’t need to run as fast. This is achieved by rapidly cycling the pump on and off to achieve the desired pump speed. VFDs present an interesting alternative to this method, using voltage and frequency instead of amperage to control the motor’s operation. Using voltage and frequency together allows greater control over a motor’s speed and torque, helping motors last longer while minimizing energy waste.
VFDs also work better and retain efficiency better than VSDs when motors are running at lower capacity. Additionally, VSDs can introduce harmonic distortion into systems that affect power quality for cooling systems. They can also overheat when operating at reduced speeds, which can necessitate extensive maintenance and potential down time. For these reasons, data centers that require constant uptime should consider CDUs with VFD motors. Data center managers also need to make sure that their CDU motors are concurrently maintainable, meaning that they can be replaced without the CDU going offline and interrupting the liquid flow to the IT equipment. While redundancy is always important for CDU motors, the reliability of VFD motors means that fewer redundancies might be necessary for VFDs than VSDs.
More Is Not Always More
While data centers require 24/7 uptime, adding multiple redundant motors can add failure points to a cooling system and running many pumps simultaneously hurts the partial PUE of the system as a whole. An alternative approach is to have one pump that is able to do all the cooling, and one backup to pick up slack in case of maintenance issues.
Both VFDs and VSDs allow for varying flow rates of a pump, but with VSD control, pump voltage is cycled rapidly to get the desired speed. This can create large current spikes affecting system power quality and in some cases can create large fluctuations in liquid pressure that need to be managed with additional diaphragm or bladder expansion tanks. To compensate for this, CDUs with VSD controlled motors often have additional pumps added not just for redundancy but to ensure that cooling demands are met over a wide liquid flow operating range. Operating more pumps than necessary, in many cases, leads to inefficiency in power consumption and increases the overall failure domain of the solution.
In addition to the motor type, data center managers should look at the coupling methods within CDU pumps. Magnetically coupled pumps with VFD motors are extremely unlikely to leak and are very reliable, minimizing the need for multiple redundancies and lowering energy use. When pumps are magnetically coupled, as opposed to mechanically sealed, components can be physically separated, minimizing mechanical vibrations and preventing wear and tear. Additionally, the separation between the drive shaft and pump components allow for a completely sealed enclosure on the pump’s liquid end. This removes another potential failure point by eliminating the need for a mechanical seal between the motor drive shaft and liquid-carrying components.
Equipping a data center with the right CDUs to power next generation liquid cooling is absolutely critical to the functioning of future data centers. Examining motor control and coupling methods for CDU pumps is just one piece in a complicated equation, but it should not be ignored, because when the liquid stops flowing, the IT equipment shuts down.
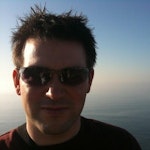
Matt Archibald
Matt Archibald is the Director of Technical Architecture at nVent supporting the data center and networking space. Matt is deeply focused on liquid cooling (close-coupled and direct-to-chip), unified infrastructure management, data center monitoring, and automated data center infrastructure management. Previously, Matt was the Global Installation & Planning Architect for Lenovo Professional Services and spent over 15 years in the data center space. Previous to this, Matt worked as a development engineer in the IBM System x and BladeCenter power development lab doing power subsystem design for BladeCenter and System x servers. Matt holds 62 patents for various data center and hypervisor technologies. Matt has four degrees from Clarkson University in Computer Engineering, Electrical Engineering, Software Engineering, and Computer Science and a Bachelor of Engineering in Electronics Engineering from Auckland University of Technology.