Last week we launched our article series on how to choose the right diesel backup generator technology. In this article, we'll explore the concept of no-load maintenance.
The usual practice for exercising your diesel generator has been to run them at 30% load, often using a load bank, for 30 minutes per month. This cycle makes sure that the engine and peripherals get up to full operating parameters and is sufficiently long to prevent the phenomena known as “wet stacking”, which is when unburned fuel, soot, moisture, and carbon are deposited in the exhaust system of the generator, reducing the efficiency and performance of the system and potentially leading to system failure or engine damage. The cause is well-known, not getting the engine to the optimal temperature and load where fuel is burning properly.
However, there are a number of changes to modern diesel engines that can potentially prevent wet stacking and allow only a single, annual test run to optimal temperature and load. Some of these changes in the manufacturing process improve operating efficiencies and minimize ring gap, which reduces the ability of unburnt fuel to escape. Less blow-by means that the engine is burning more efficiently and reducing the opportunity for stacking to occur. Common rail fueling has improved the efficiency of fuel delivery, allowing it to be more carefully tuned to the operation of the engine, a process known as fuel mapping.
Other changes include techniques such as charge air cooling, which allows more air delivery to each cylinder at a lower temperature, again allowing more efficient combustion. The combination of all these features are necessary for the no-load maintenance technique to work.
Now, instead of a monthly, 30-minute loaded operation, the monthly testing is done at no load, to test operational issues, and only a single, annual, loaded operation test is performed. This results in as much as an 86% reduction in the creation of pollutants such as greenhouse gases, and an over 40% reduction in particulate matter, using a 3250 kW load banking cycle. The full 30-minute cycle running monthly also burns over 660 gallons of fuel annually, compared to the under 300 gallons consumed by 11 months of no load testing and one month loaded annually. It is important to note that not all diesel generators are rated for this no-load testing cycle and it is critical to talk to your vendor before moving to this model as not to void any warranties.
To really maximize a commitment to sustainability, it is possible to run your diesel generators on HVO fuel. HVO, which stands for hydrotreated vegetable oil. HVO is more efficient than first generation biodiesel fuels and is approved for use by the top three backup generator vendors in the data center market. It is a fully renewable resource and produces less greenhouse gases and other pollutants when compared to traditional fossil diesel. Because its cetane number is higher, it burns more efficiently and can potentially result in better engine performance.
Important for data centers, HVO also has a longer shelf life than traditional diesel products, a very significant point for backup generators, and because it burns more cleanly than traditional diesel it can reduce maintenance cycles for the backup generators and make consumables, such as filters, have a longer usable life. HVO fuel is currently more expensive than traditional diesel fuel, but as more consumers move to the technology, the prices will come down. It’s also not a new technology as it has been in mainstream use in Europe for the last decade.
The key to building a sustainable backup power supply for the data center is clearly a combination of making use of the latest technologies and operational techniques with your power generation.
Download the full report, Choosing the Right Technology for Diesel Backup Generators, featuring Kohler, to learn more. In our next article, we'll explain diesel tier certification.
About the Author
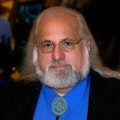