Supply chain pressures are very real for the data center industry, prompting a variety of strategies to manage inventory of hard-to-find equipment. While most operators say they have not seen major project delays, the shortages and their impact vary across geographies and types of equipment.
In recent weeks, many data center executive teams have addressed the supply chain problems during quarterly earnings calls, providing insights into the industry response.
“The supply chain continues to pose challenges for us and many, many others in the industry,” said Rob Johnson, CEO of data center equipment specialist Vertiv. “Each of the regions are experiencing it, but it is most acute in the Americas, where material availability is most difficult and commodity prices have risen beyond expectations.”
“Europe had some supply chain issues over the summer, but a lot of that has been worked out and we’re delivering,” said Marc Ganzi, the CEO of DigitalBridge, which has been in expansion mode with its Vantage Data Centers and DataBank brands. “Here in the U.S., we’ve seen similar issues, and it’s always small components that you don’t see coming that literally can slow down the actual delivery of a data hall.”
“We have seen I would say 10 to 12 weeks increase in supply chain or lead time on some of the MEP and related equipment, even including steel in some markets,” said William Meaney, the CEO of Iron Mountain. “We are seeing a lengthening of the supply chain, but I would say for 2022, we’re well covered because that’s already been addressed in committed contracts to do that build-out.”
Project Delivery Continues at Scale
Significantly, data center developers have continued to deliver new projects, with some of the largest players continuing global deployments.
“On a year-to-date basis, our global design and construction teams have delivered more than 18,000 cabinets of retail capacity, and 40 megawatts of xScale inventory,” said Keith Taylor, Chief Financial Officer at Equinix. “We’ve seen no major delays today with delivering new capacity, despite general market concerns related to supply chain challenges. That’s a reflection of the efforts put forth by our best-in-class procurement and strategic sourcing teams.”
For most data center operators, managing the global supply chain crisis has been a function of leaning hard on their experience and relationships, and getting even more obsessed about planning. Some of the key strategies include:
- Ordering equipment ahead of time.
- Holding more equipment inventory in warehouses.
- Working with more suppliers, including new suppliers who can source hard-to-find products.
- Making spot purchases to meet specific short-term demand, sometimes at premium prices.
- Doubling down on supplier relationships and financial strength.
- Working ahead on forecasting and procurement for 2022, 2023 and beyond.
Ordering ahead
There’s major uncertainty about when the supply chain pressures might ease, so ordering ahead is a top priority.
“The bad news is that the lead times have increased,” said Meaney. “The good news is that we’ve got the time to make sure we incorporate that into our planning. We’re already looking at 2023 and we’re factoring in that extended lead time for some of that equipment in our planning.”
Switch raised its capital spending by $25 million in the last quarter to order more power and cooling equipment for its expansion projects in 2022 and beyond.
“We adjust our expectations for the potential of a longer supply chain,” said Thomas Morton, the President of Switch. “What we have done is place the orders earlier to both help our demand curve and also make sure that our suppliers had adequate time to provide us the equipment that we need without delay. We have very long-standing relationships with our supply chain manufacturers. We do custom builds, so they go in a different supply chain than just the commodity products. They’re very long lead time items, and we’ve been able to plan and order those items a long time ago.”
In the current environment, Switch founder and CEO Rob Roy believes the company’s reliance on custom data center equipment is an advantage.
“When you look at the supply chain, all the other data center providers are looking at the same three or four vendors that you get products from,” Roy said at the company’s Investor Day Nov. 15. “Those are also the same three or four vendors that the cloud providers buy products from, and the cloud is not going to slow down for the next 10 years. They are absorbing all that’s coming in now and could start to say ‘hey, we’re want to buy all your production slots for a year.’
“That’s really dangerous for the rest of the data center industry,” said Roy. “Everything we do is custom made. We don’t have a single product that we buy that comes off the shelf. I’ve changed all the designs of manufacturers 100 percent, just for us. No one can come and take my air conditioner slots because those factories only make them for us. So we have a supply chain advantage over everyone else.”
Holding More Equipment Inventory in Warehouses
As companies order ahead, they need to think about where to store that additional equipment inventory and position it for future projects.
“What we are seeing is that customers are willing to take that inventory, in some cases in warehouses, so they have it when that site turns on and don’t lose their production slot or lose their equipment to somebody else,” said Vertiv CEO Johnson. “That’s more of a new phenomenon. More and more of our large customers are wanting some type of program to have inventory, so they can go ahead and take it off our hands and take the responsibility for it.”
Rob Johnson, the CEO of Vertiv.
CyrusOne interim CEO Dave Ferdman said the company has “not experienced any significant near-term headwinds.” The company was an early innovator in ordering ahead and storing equipment to speed delivery times. That experience has proven handy amid the supply chain constraints.
“We have a robust and flexible supply chain that is designed to mitigate a lot of this risk,” said Ferdman. “Our key vendors hold inventory until we need it, and we have forward purchase contracts on long lead time items with fixed rates to help protect against near-term pricing pressure.”
Working With More Suppliers
But CyrusOne has made some changes to adapt for shortages and longer lead times.
“We’ve expanded our supply chain base, in some cases to 3 or 4 providers of that equipment to diversify some of that risk,” said John Hatem, Chief Operating Officer for CyrusOne. “We’ve been focused on this for the past 4 quarters, because we saw some of this coming in our conversations with (suppliers). It’s been focused across-the-board to make sure that we have enough (equipment) to meet the demand and the time lines of the customers.”
Making Spot Purchases for Key Requirements
COVID-related factory shutdowns in Vietnam and other key production hubs made it difficult to acquire fans, circuit breakers and IGBTs (semiconductors for power switching), according to Johnson. In some cases, the best option was to look outside of the usual network of suppliers and be open to paying higher prices.
“We’ve experienced some commodity and freight inflation,” said Johnson. “We made spot buys, so that we can meet the delivery commitments we’ve made to our customers, and we have implemented strategies to recapture those costs.”
But there are limits, said Johnson.
“The market is tight for everybody,” said Johnson. “There’s been instances where somebody had to have something, and maybe a competitor willing to jump the line and knock another customer out. We’ve been very honorable with what we’ve told our customers, and we’ve not played that game.”
Leaning on Long Relationships, Financial Strength
The most-mentioned supply chain topic for data center operators has been supplier relationships, followed closely be the experience of internal procurement teams.
“We have long-term relationships with key suppliers and we benefit from having a standardized design,” said Ferdman. “That standardization, combined with the significant development that we have across the portfolio, allows us to purchase at scale and achieve better pricing. We also have resiliency built through the supply chain, with key components dual-sourced.”
Equinix CEO Charles Meyers in one of the company’s familiar blue-lit data centers. (Photo: Equinix)
“I think our team has done a just an exceptional job navigating the current realities as it relates to supply chain,” said Charles Meyers, the CEO of Equinix. “Our bottom-line message has been and continues to be that we really aren’t seeing any meaningful negative impacts to our business. But that doesn’t just magically happen. It happens by our team doing really great work to go and make sure that we are mitigating the risks that are out there.”
Digital Realty CFO Andrew Power noted the benefits of scale. “Given our track record, and our size and scale as the largest developer, we’re going to fare better than our competitor set and especially any newer incumbents to development,” said Power.
“We’ve been great to our vendors for 27 years,” said Ganzi of DigitalBridge. “Having good relationships with vendors, where you pay them on time and early, allows you to get to the front of line. We’ve actually had no issues related to labor and delivery of our infrastructure here in this hemisphere.”
Beyond The Data Center: The Chip Factor
The semiconductor industry has been hard-hit by the supply chain issues, creating shortages and delays for a everything from cars to appliances to servers. Ganzi noted that having a data hall ready doesn’t mean that customers can immediately start rolling in the chips, servers and switches to fill the space.
“From a construction perspective, we’re not seeing any choke points in the physical construction,” said Ganzi. “But when you get into the actual data center and people are lining up servers and connecting, that’s where we’re seeing some of the supply chain issues materializing today.”
The recent earnings commentary from IT equipment leaders confirm that component availability crisis continues to impact operations.
“Overall, the server business is constrained by supply,” said Pat Gelsinger, the CEO of Intel. “Trust me, we would be shipping a lot more units if we weren’t constrained by the supply chain of these other components in the industry. Our customers, both cloud customers and OEMS, very strong backlogs that they’re pressing us aggressively to satisfy.”
“The server business is constrained by supply. Trust me, we would be shipping a lot more units if we weren’t constrained by the supply chain.”
Pat Gelsinger, CEO of Intel.
“We are clearly in the midst of an acute supply chain crisis with increased prices and long lead time,” said Jayshree Ullal, the CEO of network gear vendor Arista Networks “Lead times of many components have extended to 50 to 80 weeks, with price hikes ranging from 15% to as high as 200% across our entire supply chain.”
In a number of earnings calls, securities analysts pressed data center executives about whether chip shortages were slowing the “fill rates ” at which tenants occupy leased space.
“We haven’t experienced any customers doing significant delays or sharing with us they’ve had significant delays in their need to obtain items to deploy in our facilities,” said Morton, the President of Switch. “They have been deploying on time and on pace. So we haven’t seen much in the way of a supply chain impact at least to date in our operations.”
“We talk to our customers all the time, and we haven’t had anybody say, ‘listen, we’re not taking the capacity because we don’t have chips.'” said Hatem, the COO of CyrusOne. “Our big enterprise and hyperscale customers are really doing the same thing we’re doing by pre-purchasing chips and the things that they need to run their business.”<
But signs of slower buildouts may be showing up in the budget for Loudoun County in Virginia, where tax revenues from data center equipment are expected to fall about $60 million short of expectations for 2021. County staff say there may be several reasons why their projections are off, but that slower installations by data center tenants is one explanation.
About the Author
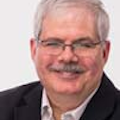